Infrared inspection of your fired equipment internals or furnace tubes is one of the most difficult of infrared tasks. Specialized equipment and training is required for accurate measurement and interpretation of the results. Infrared Thermal Inspection has the experience and expertise with some of the most qualified technicians in the industry.
Furnace tube inspections can help identify problem areas such as flame impingement, internal fouling or coking, and failing thermal indicators. This information can help extend run times and protect the life of your tubes.
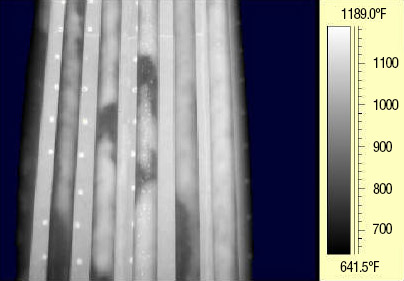
Often thermal indicators do not function properly or the placement may not be in the affected area. Internal deposits can go unnoticed causing damage to your tubes. Flame impingement and improper operations are also included in our furnace inspections. Infrared inspection of your tube surfaces can give you a better understanding of the conditions that affect tube life so adjustments can be made in a timely manner.
We have the expertise to correctly diagnose and help you make adjustments to extend run times and protect your equipment which translates to major savings!
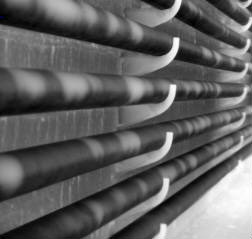
Localized internal fouling can go unnoticed by operations personnel using thermal couples as the only source of tube temperature indications.
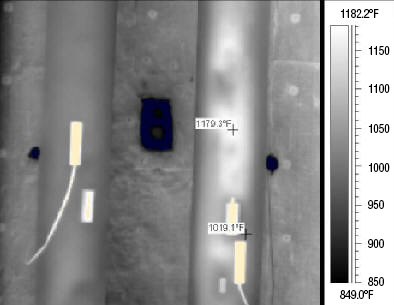
The above image shows internal fouling only inches away from a correctly operating thermal indicator. Control board reading showed operations a maximum tube temperature of 1018 F.
Once internal fouling becomes severe, deposits act as in insulator preventing heat transfer to the product and raising tube metal temperatures above design limits that can lead to failure.See Steam Air Dekoing Services for removal of internal fouling.