Download a PDF copy of this resource.
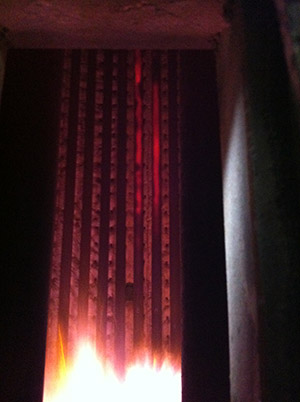
Since the inception of mechanical decoking or “pigging” in the 1990's, many equipment owners have moved away from the traditional steam air decoke. The truth is steam air decoking is still a valuable resource for removing combustible material from ID surfaces of fired equipment. Steam air decoking has seen a comeback in recent years as equipment owners have noticed significant changes in the way their units behave and how often they have to come down for unscheduled maintenance. Until recently it has been reserved for equipment with common headers or multiple diameter tubes that would not allow for mechanical cleaning. Often stories of equipment damage feed equipment owner's fears of the possibility of damage as a result of utilization of this technique to decoke their equipment. As consideration about the reintroduction of steam air decoking of fired heaters in fouling service has reemerged, the tales of the “burn out gone bad” in years past have often been the first item up for discussion. Although some make for great story telling, most are exaggerated and leave out the primary cause or causes of damage to the equipment. Properly executed, a steam air decoke can be the solution to problems of decreasing operational periods between necessary coke removal and more strict maintenance schedules. With additional knowledge and advancements in technology, steam air decoking is safer and more efficient than ever.
Steaming or spalling of the tube ID is not better than burning. Many feel that removal of as much material as possible is better than removal during the burn. Erosion of u-bends is the major concern with steam velocity. Thin layers of coke in the u-bend help protect the tube metals from steam cutting or erosion and would typically be the first coke removed during a spall. The most important thing to consider during spalling is the possibility of erosion and take steps to minimize or eliminate it. One common error is the use of high steam volume and pressures for extended periods of time in preparation for a steam air decoke. Equipment in an open configuration will create much higher velocities at similar pressure than a closed system.
Light spalling with observation of the discharge is the best way to prepare the heater for the burn process. Shocking of the tubes in certain temperature ranges can aid in fracturing the coke deposits to aid in ignition, but must be controlled within allowed temperature ranges. An experienced technician will observe the effluent looking at volume and consistency of coke particles to determine when air should be introduced. With complete control of tube metal temperatures and pressures, the only variable realized from a steam air decoke when compared to normal operation is steam velocity. The potential for u-bend damage can be reduced significantly by minimizing spalling and performing the procedure at low inlet pressures. Often ultrasonic thickness testing is performed on tubes only after the decoke process. When erosion is observed, it is often just blamed on decoking in general. UT inspections of u-bend outside diameters should be completed prior to and after decoke when possible for signs of damage and the procedure can be adjusted accordingly. Additional inspections such as replications, and various other metallurgical tests performed by clients have concluded that a properly administered steam air decoke can have little or no detectable effect on tube thickness or grain structure, including u-bends. Removal of tube sections post decoke for internal inspections show smooth polished surfaces almost mirror like in appearance. A secondary concern of excessive spalling and shocking of tubes would be potentially plugging the tube with coke. This would be an additional argument for using minimal steam as for maintaining flow until the decoke technician observes the conditions of the heater and effluent.
One of the common methods for decoke control is the use of thermal indicators attached in various locations and coil outlet temperatures used to control movements during a decoke burn. While these can be useful additional information, they can also mislead personnel into making adjustments to the heater that can be detrimental to the tube materials or the quality of the decoke process. Infrared technology can see all or most of the tubes in the radiant sections of the heater and give accurate data that can be utilized by qualified personnel to make the correct changes. Conservative decoke methods and thermal couples may be utilized when burning through the convection pass is desired. The decoke procedure can be slowed and the technician will watch for the emergence of burn indication to exit the convection and enter the radiant tubes before continuing with an optimized procedure.
Some say there is no “proof” of the state of the equipment at the completion of the decoke procedure. ITI typically utilizes a proof burn phase where all steam is removed from the heater for a period of time and tube metals are raised to maximum allowable limits. During this stage, any combustible materials would burn and can be seen by infrared equipment to ensure the area does not exceed allowable temperature. Additional information can be obtained by operations if desired by sampling the air for levels of oxygen and carbon dioxide to ensure when or if burning is occurring. Infrared images recorded throughout the burn phase will document where burn indications begin and when they are no longer present. Pre and post decoke infrared inspections can illustrate the effectiveness of the decoke whether by mechanical means or steam air decoke.
While there are true stories of damage to equipment during decoke, it can be shown that excessive spalling, excessive temperature, poor procedures, and inexperienced or not properly trained and equipped personnel account for these failures and are compounded by condition of the tubes at the start of the procedure and/or limits placed by poorly designed steam/air controls to the heater and limitations on available resources.
Many reported failures have been the result of operations personnel utilizing an optimized decoke procedure in the absence of the qualified decoke technician. All of these issues are correctable with the exception of existing damage.
The truth about steam air decoking.
Clients report the return to historical run times after returning to at least partial steam air decoke schedule. Polishing of tube ID surfaces help reduce the ability for materials to attach to the tube walls. While deformation of the tube, changes in tube sizes, and other design issues may affect the quality or the ability of a mechanical cleaning, they do not affect the steam air decoke process. Incomplete removal of coke material will decrease the run for the following operational period. Complete removal along with polishing of tube ID surfaces will extend run times reducing the additional expense of unit shut downs for decoking only allowing for more total run time! In some instances we have seen run times increase from 3-4 month intervals with mechanical cleaning to over 12 months with a return to steam air decoking and the addition of a comprehensive inspection program to address contributing fouling issues such as burner cleaning and heat balance issues along with early identification of localized fouling indications.
Non-combustibles can be removed. Most calcium, silica, salts, coppers, sulfur and other non-combustible material will be released from encapsulation in coke and carried in the effluent. While it is possible for some to remain in the tubes, depending on tube ID condition (smooth tubes will release easier while rough or scratched tubes can aid in attachment) and location of the deposit (tube wall vs. encapsulated), it is usually not of concern. A follow-up infrared inspection can determine if there are any remaining insulating materials and how they affect tube metal temperatures. Mechanical cleaning may be recommended for removal of these materials on a rotating schedule, depending on the severity and type of process.
A properly administered steam air decoke procedure can be done safely, in a timely manner, with no loss of material from tube surfaces and no reduction in tube life. The key is making sure you have the right tools and the right people for the job and a quality procedure that allows for the safest most efficient decoke possible. Additional benefits can be realized from reduction of personnel and quick turnaround times. Emergency decokes can be completed in as little as 24 hours from oil to oil in some instances, with the typical turnaround time of 36 to 48 hours easily achievable . Total time required can vary based on available resources (steam and air), design (piping sizes, restrictions), consistency of internal deposits, and limitations due to inefficient procedures. Decoke time can be reduced by giving qualified personnel the ability to adjust as needed to ensure the combustion of material is never allowed be slowed by steam and maintain as much oxygen as tube temperature limitations will allow. Tube metal temperatures become the control in this method rather than a clock. This will not only safely increase the speed, but will improve the quality of coke removal as well.
Example Steam Air Decoke Time Table
Cool Down and flush = 10 hours
Blinds/u-bends = 4 hours
Decoke (typical) =12 hours
Cool down = 8 hours
Blinds/U-bends = 4 hours
Return to service
Total time involved = 38 hours
While it is common to see estimates of up to 48 hours for completion of the decoke portion alone, often the current procedure or inadequate planning are the only limitations preventing completion in as little as one shift. Through optimization of procedures and using only qualified personnel, decoke times can often be reduced by 50% or more from the typical in house procedure. With available resources multiple heaters and/or passes can be decoked simultaneously. A typical 4 pass Coker charge heater should take approximately 18-20 hours for completion of the decoke portion of the maintenance schedule while a smaller HDS (Hydrodesulfurization) heater can be completed in 6-8 hours. Regeneration of catalyst of a steam methane reformer may take up to 36 hours.
Pigging vs. Steam Air.
Although many choose one side or the other like a “taste great” or “less filling” commercial, both technologies have positive and negative attributes associated with them. Both are highly dependent on the quality and experience of personnel, both can be completed in similar amounts of time, and both can achieve acceptable results that vary from process to process and heater to heater. Infrared inspections following mechanical cleanings reveal that internal deposits can be left by mechanical pigging, even if the chart shows no loss of contact with the walls while steam air can potentially leave non combustibles. While it is possible to damage u-bends during a steam air decoke if too high steam velocities are used, scarring of the tube ID is not. You can't get steam or air stuck in a tube either. Claims of higher speed by mechanical cleaning are not always true, they depend on the project. With little or no damage to tube metals (only if both are conducted properly) it's a wash. Cost is harder to compare. Pigging has a cost structure that can be easily be seen. Steam air decokes have costs that cannot be as quickly calculated in steam, air, and fuel gas usage. Charges for 3rd party decoke control are generally less than 25% of a mechanical cleaning crew and equipment charges. After adding in the cost of resources, steam air decoking is still very competitive with potential added benefits. While pigging has been around for about 20 years, steam air decoke has been there from the beginning. Advancements in technology and understanding gained have improved both methods considerably. So which is better? Ultimately the choice should be made based on your equipment design, tube condition, process, available resources, and intended results rather than unsubstantiated or outdated claims and half truths. Modification of decoke procedures will often make steam air decoking the preferred method of coke removal.
If unit downtime costs a conservative $15,000 per hour in lost revenue, removing one decoke annually could save an estimated $1.8 million dollars per year or $18 million over a 10 year period! Reducing a single outage time by 24 hours will save $360,000 in lost revenue. How much does your unit loose per hour while not in production? Don't forget to add in the cost of reduced production of other units affected by your unit. A typical ITI infrared inspection program for one unit with 4 average size heaters and two steam air decokes is estimated at approximately $60,000 annually. That's a potential >3000% return on investment before you add in reduced potential tube failures and unplanned shutdowns.
IT Imaging utilizes one technician (per shift), one client operator, and process board control for the procedure, freeing up your personnel for other duties and no bulky equipment to take up valuable turnaround space is needed. ITI has extensively trained personnel who have performed hundreds of decokes with zero incidents! As much of the generation of operations personnel that are familiar with decoking have retired or are no longer in field positions, and many that remain only assisted the more experienced operators with the procedure 15 to 20 years ago, the need for experienced decoke technicians has grown. ITI lead technicians have between 10 and 20 years experience and will typically perform as many steam air decokes annually as most operations personnel would be exposed to in their career. This gives the client access to knowledge gained from multiple heater types and processes and with much more exposure than an operator that may decoke 1 or 2 times annually. Equipment owners provide the engineering limitations for tube metal allowable temperatures and our personnel will ensure that these limits are maintained. Procedure reviews and recommendations are included with our service to create a customized procedure that offers the greatest equipment protection with the most efficient decoke for your equipment possible.
If you are considering or currently use steam air decoking, we would be happy to discuss any questions or concerns you may have. Contact Infrared Thermal Imaging, Inc. at 1-877-484-6244 to discuss how we can help with your fired heater inspection and/or decoking needs.